今朝のブログは、2013年に張 トヨタ名誉会長と池渕 顧問・技監が、トヨタグループの基幹職向けに対談された時の、私のメモから貴重なお話を皆さんにお伝えします。
(ところどころで、私の解説を入れてあります)
フォーラムに掲載する予定でしたが、多くの方々に読んで頂きたいと思い、春の連休に考えていただく材料として、お送りいたします。
TPSは大野耐一元副社長が生みの親と言われていますが、張名誉会長と、池渕顧問・技監は、それを大きく育てた第2世代の方々です。
私がTPSやマネジメントなどをご教授していただいた、内川元会長(現 東京電力特任顧問)とともに、現在のトヨタの競争力を育てて来られた方々です。
この時の対談は、次世代のリーダー向けにお話しされたものです。TPSの基本のお話は、いろいろな本で紹介されていますが、この場でお二人から伝わってくるエネルギーを感じることができたのは、私にとっても幸運でした。言語で語れないほどのものすごい臨場感を感じました。
大野さんは「TPSに完成はない。どこまで行っても新しい挑戦がある」とおっしゃっていました。
すこしづつ変えていく、トヨタウエイにある絶え間ないカイゼンをどこまでの続けて行くことが、TPSなのです。
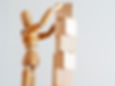
戦後の金融引き締め政策(ドッジライン)により、大量倒産、失業が起こりました。トヨタもトラックが売れなくなり、倒産寸前になりました。
人員削減をおこなって、労働争議によって喜一郎社長の退任まで引き起こしてしまいました。
こういう経験があって、造りすぎのムダが最大の罪であることを強く認識しました。TPSで7つのムダと言っていますが、ムダの中の最大のムダが、造りすぎのムダだという結論です。
この頃国内の他の自動車メーカーは、フォード等 外国メーカーとの技術提携を行いましたが、トヨタはお金がなく、技術提携を断念せざるを得ませんでした。チャンスを逃してしまったということもできます。
”トヨタ本”では、トヨタの自前主義と言われていますが、お金がなかったというのも、トヨタが外国企業と提携しなかったことの理由の一つであったようです。
お金はなかったが人はいました。トヨタは身の丈よりも2~30倍の人を採用。これが今日の基盤を造ったと考えて良いと思います。
独自の技術を開発し、労働組合との関係を立て直し、財務基盤を健全化していきました。
この頃の地に足のついた活動、自らのやり方で、健康な企業体質を育んでいきました。
製品開発では、中村主査を始め、初代カローラ長谷川主査、レクサスの鈴木主査、プリウスの生みの親内山田主査などの話を私のフォーラムに掲載してあります。

その当時のフォードはプッシュ方式で、手直し専用のラインがあり、そこは手直し待ちの車であふれていました。
トヨタは、お客さま第一を掲げ、「1台売れたら1台作る」という考え方を根本に据えて、プル方式を考えました。これが在庫を極力持たないという、少ないお金で会社を回していく方法に育っていきました。
1960頃からトヨタでは組立でジャスト・イン・タイムを採用しました。
現在では、これがトヨタの工場の当たり前の姿になっていますが、タクトタイムにより自律的に生産ラインが進行し、各工程が完全に同期しています。
流れ化することで、さらにムダが見え、カイゼンが進むという生産方式です。
それに加えて、再発防止を徹底的にやるなどの活動を行いました。
「トヨタの問題解決」に代表されます。一般的には「なぜなぜ分析」「5なぜ」などと言って知られています。
問題が見つかったら、その根源まで遡って、原因を見つけて、作業のやり方をカイゼンして、作業標準書に折り込んでいくという方法です。
大野さんが、TPS生みの親と言われています。その教え子にあたる張名誉会長は、第2世代となります。第2世代に回された役割は、外注メーカーへTPSを広めていくということでした。
例えば、池淵 顧問・技監は入社したての頃、大野さんから「豊鉄へ行って来い」と言われました。
「むこうでうまく回るように、そのプロセスを直す。トヨタ都合ではだめ。できるまで帰ってくるな。」と言われ、3ヶ月の予定が3年かかりました。
その頃の現場は職人気質で、1ヶ月まとめて仕掛け屋(事務屋)が生産計画を出しますが、それを見ずに、現場は勝手にやっていました。
技術員室ができ、かんばんの仕組みができました。生産計画を仕掛け屋が作っていましたが、かんばんで自律的にラインを流すことになると、ラインがストップした時の責任は全部現場になります。これで職場に力が付きました。
販売の状況に対して、製造はいかに流動的に対応できるかを追求して行くことが重要です。
市場は流動的ですが、製造は固定的になってしまいます
製造は出来る限り流動的にやる体制を作ることを目指します
変化に対応する工程は、標準作業とタクトタイムをベースとして編成します
変動に対し、出来る限り造り方を変化させて対応することが基本です
変動に対し、在庫で対応する部分を減らすという考え方が基本です (1個流し、小ロット、段取り替えを短縮)
予測は当たりません
難しい予測を避けるため 出来るだけ生産のL/Tを短縮する
例えば、かつて、鉄板のL/Tは3ヶ月でした。3ヶ月前に発注しないと鉄板が間に合いませんでした。鉄鋼メーカーに掛け合っってL/Tを短縮してもらった
海外から調達するともっとL/Tがかかります
(前工程)生産の前にお客様と直接つながる販売があることは大切なこと
(後工程)関連メーカーがどういう状態なのかを知っておくことは重要
日本は欧米と比較して1/10くらいの生産性しかありませんでした。トヨタでは、トップから3年で追いつけと言われました。
その当時のフォードはプッシュ方式で、手直し専用のラインがあり、そこは手直し待ちの車であふれていました。
プッシュ方式だと、どんどんモノが来てしまって在庫が増えてしまうので困ります。品質確保のため止めるという逆転の発想で、流れ生産の考え方を確立しました。
フォード方式では、膨大な手直しラインが必要となします。常に不良が起きたときの人員を構えています。
当時のトヨタはフォードの1/100の生産台数しかありませんでした。トヨタ独自の方式(フォード+JIT+自働化)を完成するのに、結局20年以上かかりました。
80年代に比べれば競合メーカーも強くなっています。韓国の会社もトヨタ以上のところがあると言われています。
TPS手法だけではだめで、TPSとトヨタウエイ(行動規範)の両方が合わさって初めて機能する。会社全体で言えば、さらに製品開発の力が合わさることで力となります。
それをスパイラルアップして、その時々の状況を見極めながらフレキシブルな対応をする必要があります。これまでに確立してきた基本の軸を守りながらフレキシブルに対応することが求められています。
日本人にはカイゼンが当たり前。アメリカに進出したとき驚いたことは、アメリカではカイゼンという概念がありませんでした。
Improvementでは通じませんでした。
フォードは4年に一回大きく変えるという習慣しかありませんでした。
"Daily Continuous Improvement"と言わなければアメリカの人たちにはカイゼンということばが通じませんでした。
1970年代半ばのオイルショックの時は、販売は国内が中心でした。TPSも始まったばかりでしたが、在庫がないから問題がすぐ見えるので、すぐに手を打つことができました。
2000代終わりに起きた、リーマンショックでは、トヨタの兵站はずいぶん伸びていました。L/Tが伸びていました。そのハンデを補うことができていませんでした。レスポンスが極めて悪い状態でした。
個々の力は同じだったが、つなぎが不十分でした。現在は早く対応することが出来るようになってきました。
人をレイオフしないということを明確に約束したことはありませんが、レイオフは最後の手段です。
如何に危機に対して対応策を考えて、それをやりきるかが大事です。この考え方は世界共通で、アメリカの労働組合からも評価されました。
TPSは一時マンネリに陥りました。
しかし、原点を忘れないことで今を迎えています。
1個流しが原点です。現在はプレスや鍛造など素材までさかのぼって、1個流しをやっています。
最後に、「事務技術部門はどうか?」という質問に対し、超名誉会長のお考えを紹介します。
「事務技術部門は問題が上がってこない。もっと問題を早く出せるようになれば良いのだが、そこがTPSの出来ていないところ。全体でみてもTPSの完成度は7合目程度。まだ30%は延びる余地がある。事務技術部門はうまく出来ていない。大野さんに『(事務技術部門は)張がやる。』と言われたことがあった。」
いかがでしたでしょうか?
もっと詳細な記事は、私のHP内のフォーラムに沢山掲載してあります。
今始まっているグレートリセットは、私たちにもオイルショックやリーマン級の大きな影響があると考えています。今のところ2024年4月には、新札を発行するということになっています。
今始まっている半導体の問題をトヨタがどう対処しているか、すでにインサーダーではない私にとって具体的に知る由もありませんが、2日前のブログでも書きました通り、「在庫は必ずしも「悪」ではありません」、基本を忘れずに柔軟に対応することを行動に移しているはずです。
危機の旅にもっと成長するか、じっと耐えるだけなのかが、
企業の将来を大きく変えていきます。